世界標準のSCM用語解説
米ASCMのサプライチェーン用語をコラム形式で紹介します。ASCMが編纂したSCM用語辞典(第17版)の翻訳チームに所属するメンバーの有志の方々に監修いただき、SCM用語辞典(英文、約5000語採録)より、特にロジスティクス分野と関連の深い用語を選んで「定義(和文・英文)」「事例」「意義」を世界標準のSCM用語解説と題してご紹介します。
サプライチェーンは地球発・地球着の「グローバル」な世界観が基本です。ここでは世界最大のSCM標準化推進団体である米ASCMの知識体系に基づく用語法-共通言語のうち、特に重要と思われるものを取り上げます。
目次
- SCM用語#1:「MP&C」
- SCM用語#2:「ASCM」
- SCM用語#3:「SCOR-DS」
- SCM用語#4:「CSCP」
- SCM用語#5:「S&OP」
- SCM用語#6:「ROIC」
- SCM用語#7:「MRP」
- SCM用語#8:「DDMRP」
- SCM用語#9:「パーフェクトオーダー」
- SCM用語#10:「CCC」
* 2024.11.18 ロジスティクスシステム本誌に合わせてSCM用語のナンバリングを修正しました。
SCM用語解説
SCM用語#1:「MP&C」
サプライチェーンはモノ作りとモノ運びを中心とした複数の企業活動が相互に関連しながら成り立っている運命共同体としての性質を有しています。この一種の「エコシステム」をモノ作りの活動を中心において俯瞰する際の参照枠組みは”Manufacturing Planning and Control system (MP&C)”として知られています*。
MP&Cは企業内のSCMを仕入・生産・納入といったモノの流れを伴う「実行・管理(Control)」レイヤー、その活動の効果を保証するための「計画(Planning)」レイヤー、そして計画の前提となる設備投資等の判断を伴う「戦略」レイヤーからなる三層で構成されます。
それぞれのレイヤーでは短期・中期・長期の需要マネジメントおよび供給能力マネジメントを通じて供給活動の優先順位給に関する意思決定を行います。これらの意思決定は長期から短期に向かって階層的に行われる点に特徴があります。
また、MP&Cは自社内だけでなくサプライヤーやカスタマーなどサプライチェーンを構成する他の企業との間で問題状況を整理する際や課題を設定する際に用いる共通の参照枠組みとしても普及しており、SCMに携わる様々なレベルの人々にとってのいわば「共通言語」となっています**。
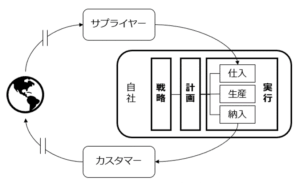
*山本圭一・水谷禎志・行本顕「基礎から学べる!世界標準のSCM教本」(日刊工業新聞社)
**山口雄大・行本顕・泉啓介・小橋重信「全図解 メーカーの仕事」(ダイヤモンド社)
SCM用語#2:「ASCM」
ASCM (Association for Supply Chain Management)は米シカゴに本部を置く非営利のSCMの標準化推進団体です。1957年に設立されたAPICS (American Production & Inventory Control Society)を母体としており*、現在も「エイピックス」という旧名称を用いるSCM実務家は少なくありません。例年9月に米国で開催される同名の年次大会には世界各国から数千人のSCM実務家が参加しており、事例・研究成果の発表や教育セッションを通じた情報交換が活発に行われています。
ASCMは様々なSCM推進団体との合併・連携を通じて活動範囲を拡大し現在はビル&メリンダ財団の支援を受けつつ世界100か国以上に約300のチャネルパートナーを擁しています。旧APICSの設立以来SCM実務家向けの教育プログラムと資格試験を提供しており、半世紀以上の歴史を持つCPIM (Certified in Planning and Inventory Management)試験を中心に現在約17万人の有資格者がいます。
ASCMの提供する教育プログラムの特徴は「ローコンテクスト」であることを重視する点にあります。**グローバルを前提としたサプライチェーンにおける企業間コーディネーションや意思決定を行う際には、前提となる事象や共有化された情報についての解釈が相互に了解されていることが重要になります。つまり、方法論においても誤解の余地のないレベルで使うことのできる「共通言語」が求められます。先述のMP&CをはじめとするASCMの知識体系は一見基礎的ですが、だれもが使うことのできる参照枠組であり、この事実こそが実務家への普及を促進してデファクト標準となった本質的な理由といえます。
このようなASCMの知識体系は多くの企業が利用しており、多国籍企業である化学会社のBASFが社内のサプライチェーン学習基盤としてASCMのプログラムを活用しているのはその一例といえるでしょう***。同社が「問題状況の把握や課題を設定する場面においてASCMの知識体系は他の部門と協力して最良の結果を得るための基礎になっている」とコメントしていることからもその様子が覗えます。
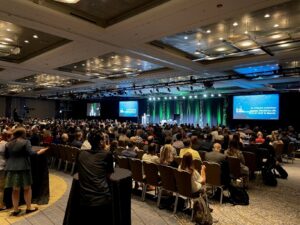
*ASCM “Supply Chain Dictionary 17th edition”
**行本顕・深谷健一郎「グローバル・サプライチェーン経営における、共通言語の重要性」
***ASCM case study BASF
SCM用語#3:「SCOR-DS」
SCOR-DSとはSupply Chain Operations Reference – Digital Standardの略で、各社各様に作り込まれたサプライチェーンの諸プロセスを以下の標準的な機能群に分類・定義し、それら相互の関連を構造的に記述するための参照モデル=共通言語です(下図)*。
①需要サイドの機能:Order(受注)、Fulfill(納入)
②供給サイドの機能:Source(調達)、Transform(生産)
③循環を生む機能:Return(回収)
④各機能を同期する機能:Plan(計画)
⑤各機能を相互に連携するエコシステムとみなし介入する機能:Orchestrate(オーケストレート)
このように標準化された共通言語で自社サプライチェーンを記述することで、より客観的かつ俯瞰的な現状分析が可能となります。
また、SCOR-DSにはプロセス毎の評価指標やベストプラクティス、必要とされる人材スキルも体系的に整理されているため、世界的バイオテック企業のRocheなど多くの大手企業からサプライチェーン改革プロジェクトの指南書として採用されています**。これにより産業毎のベンチマーキングが可能となった点もSCOR-DSの大きな貢献と言えます。
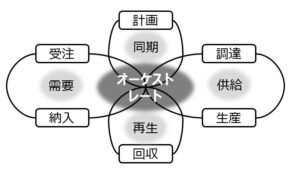
* ASCM “SCOR Digital Standard”
https://www.ascm.org/corporate-solutions/standards-tools/scor-ds/
(概念として日本語訳が馴染まない側面があるため、やむを得ず一部の語をカタカナ表記とした。)
** ASCM “CASE STUDY – SCOR Transformation Speeds Up Pharmaceutical Project Timelines for Roche”
https://www.ascm.org/corporate-transformation/case-studies/roche-case-study/
(Rocheのサプライチェーン改革は2018年に始まっており、同社が主に用いたのはSCOR-DSの前身にあたるSCOR-ver.12であったと考えられる。)
SCM用語#4:「CSCP」
CSCPとはCertified Supply Chain Professionalの略で、ASCMが提供するSCM学習プログラムの一つです。CPIMなど他のプログラムと同様MP&C(連載第1回参照)に沿って体系化されており、特にマネージャ層に必要とされる供給活動の優先順位に関する意思決定を適切に行うための観点の習得を目指す点に特徴があります。サプライチェーンを構成する個々の要素を俯瞰的な視座から意味づけることを重視する内容になっており、サプライチェーン全体にわたる広汎な知識を習得していることが学習上の前提となります。サプライチェーン・マネージャや、グローバルSCM構築プロジェクトに参画されている実務家にとり一種の「教養」といえます。
読者の中にはグローバルでの議論において、同じ単語を使用しているにも関わらず、話が噛み合わない、といった経験をされたことがある方がいらっしゃることでしょう。これは、英語などの言語の得意、不得意の問題とされがちですが、実はSCMの概念や用語法の理解に齟齬があることに起因するケースが多々あります。CSCPは、そのような状況を避けるための「共通言語」の一種ともいえるでしょう。
CSCPは2006年に始まった比較的新しいプログラムですが、すでに全世界のASCM有資格者約17万人のうち3万人超を占めています。特に日本国内の有資格者の多くはCSCPを選好していると言われています*。プログラムの内容は最新の世界情勢を反映しながら頻繁に更新されており、現在は2022年3月にリリースされたバージョン5.0が最新版となっています。
1 | Supply Chains, Demand Management and Forecasting |
2 | Global Supply Chain Networks |
3 | Sourcing Products and Services |
4 | Internal Operations and Inventory |
5 | Forward and Reverse Logistics |
6 | Supply Chain Relationships |
7 | Supply Chain Risk |
8 | Optimization, Sustainability and Technology |
CSCP 5.0のモジュール構成**
* 米国ASCM本部およびASCM日本代表部(公益財団法人日本生産性本部)ヒヤリングによる
**ASCM “CSCP 5.0 Exam Content Manualを元に作成
SCM用語#5:「S&OP」
Sales and Operations Planning(S&OP)は、サプライチェーンを構成する企業が供給計画を立案するための活動の一種です。特に供給活動の優先順位に関する意思決定を行うプロセスとして知られていま す。世界標準のSCMにおける階層的意思決定のフレームワークであるMP&C1)には他にも優先順位計画に関するプロセスとして「MRP」と「マスタースケジューリング(MS)」があります。S&OPはこれらの上位概念として位置づけられており、MSおよびMRPが短期的な優先順位計画を目指すのに対し、 中期的な優先順位計画の立案を目指す点に特徴があります(図表参照)。
S&OPにおいて考慮する主な情報として①需要計画 ②供給能力計画 ③事業計画 が挙げられます。基本的な活動としては、これらのうち①②を比較していずれかが過大/過小である場合に③に則してとる べき対応を決定します。もっとも、これらの優先順位決定に際して新たな設備の導入や取り扱い品目の 改廃を伴うことも少なくありません。このような場合には③事業計画の見直し=経営資源の再配分を視 野に入れることになります。そのため、S&OPにおいて考慮すべき情報は翌期予算編成に間に合う18ヶ月以上先を含む範囲(中期)とされています。
また、一種の経営判断を伴うことが想定されている点に関連して、S&OPにおける検討の対象は限られた時間の中で適切に判断できる件数にとどめることが求められます。たとえば、S&OPの先駆者であるボブ=ストール/トマス=ワレスはS&OPの対象とする製品グループの区分を15個前後にすべきとしています2)。このようにして需給両サイドと経営層の間で合意された供給活動の優先順位計画は「プロダクション・プラン(PP)」と呼ばれます。PPは次ステップのMSにおいてSKUレベルの優先順位計画を立案するための基礎情報として用いられます。そして、MSに続くMRPではパーツ単位の優先順位計画に分解され、さらに実際の生産・調達活動への指図情報となります。
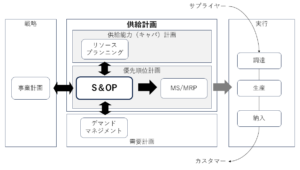
*Robert A Stahl, Thomas F Wallace “Sales & Operations Planning The Executive’s Guide”
SCM用語#6:「ROIC」
Return on Invested Capital(投下資本利益率、ROIC)は、事業等に投じられた資本に対する税引後営業利益の割合を示す指標です。金融・会計分野で用いられることの多い指標ですが、SCMにおける諸活 動の効果の有無・程度を把握するためにも用いられます。たとえば、ガートナーのSupplyChain Top 25の常連でもある飲料大手Diageo社や、食品大手Nestle社は主要な経営指標としてROICを採用・開示しています*。ROICは、次の計算式で求めることができます。
この式の要素をMP&Cに投影すると、両者の類似性が浮かび上がります。供給活動を通じて生じた売上・コスト・費用等≒利益は実行系業務に関する財務インパクトとして、投下資本は設備投資や製品 在庫政策に関する財務インパクとして把握することができます。ROICはこれらを統合的・俯瞰的に評 価し得る指標といえ**、前項のS&OPにおいて経営判断を伴う意思決定の効果の程度を把握する際に考慮すべき要素であることがわかります(図表)。
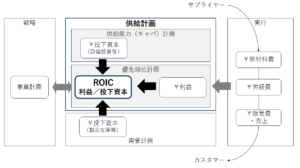
* Diagio “Annual report 2023”, Nestle “Annual review”
** 山本圭一・水谷禎志・行本顕「基礎から学べる!世界標準のSCM教本」日刊工業新聞社
SCM用語#7:「MRP」
MRPは今や広く普及した概念ですが、改めてその中身と一連の計画業務の中での位置づけを整理したいと思います。
MRPは、前工程であるマスター・スケジューリングで作成された日割りあるいは週割りの生産計画をインプットとして受けるところから始まります。この生産計画=「どの製品をいつ、いくつ作る必要があるか」から逆算して、その製品を構成する部品表、各工程のリードタイム、各製品・部品・資材の在庫量を踏まえて「どの部品・資材をいつ、いくつ作る(発注する)必要があるか」を導き出すのがMRPの作業です。
MRPは一度で完結するものではなく、アウトプット計画の実行可能性を維持するため、修正が必要になることもあります。その実行可能性を供給能力の観点から検証するのがCRP(Capacity Requirements Planning)です。CRPでは、MRPの結果に対して各工程の部品単位の製造能力が足りているかをチェックし、MRPへフィードバックします。必要な修正を経て実行可能な資材所要量計画が固まって初めて、製造工程や部品・資材サプライヤーへの発注等の実行・管理フェーズへ移行していく流れとなります(下図)。
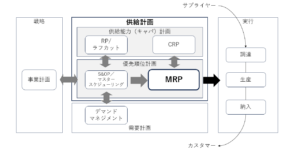
* Diagio “Annual report 2023”, Nestle “Annual review”
** 山本圭一・水谷禎志・行本顕「基礎から学べる!世界標準のSCM教本」日刊工業新聞社
SCM用語#8:「DDMRP」
DDMRPは、MRPの手法を踏襲しつつ戦略的に在庫ポイントを配置することによってダイナミックに需要の変動に対応することを狙いとする手法です。その背後にはフローを重視するTOC(制約理論)の考え方があります。DDMRPの活動は、下図に示すようにPosition, Protect, Pullの3つのフェーズに大別されます。

まず、Positionフェーズでは、顧客が受け入れることのできるリードタイム内に製品を供給するために①ボトルネックとなる部材等を部品表上で特定し、戦略的在庫(バッファ)を配置する場所(デカップリングポイント)を設定します。
続くProtectフェーズでは、②デカップリングポイントの適切なバッファ量を算出し、③この計算に用いる諸要素の増減に基づいてバッファ量を動的に調整します。このとき、バッファの水準を赤・黄・緑の三色で表示・把握する点が特徴といえます。
そして、Pullフェーズでは、④在庫と実需から正味フロー(Net Flow)を算出します。その計算結果とバッファの乖離にもとづいて生産・調達必要数が計画されます。そして、⑤供給活動上の優先順位について社内外の関係者と調整を図り、計画を実行に移します。
このように、未知の需要の変化に追随することを前提として資材所要量計算を策定していく点がDDMRPの特徴といえます。また、①において適切にデカップリングポイントを設置することで需要情報がサプライチェーンを伝播する過程で増幅される「ブルウィップ効果」*を抑える効果が期待できる点も特徴といえます。
以上のように、需要予測を起点として供給数量を決定するMRPに対し、DDMRPは実需を起点とする点に特徴があります。両者は多様な需要を前提とする現代のSCMにおいて互いを補完しあう関係にあるといえるでしょう。
* 山本圭一・水谷禎志・行本顕「基礎から学べる!世界標準のSCM教本」日刊工業新聞社
SCM用語#9:「パーフェクトオーダー」
「パーフェクトオーダー」は、ある注文に対して①全数を、②納期通りに、③正確な納品関連書類とともに、④不良無く、納品できている状態を指す言葉です*。全注文数に対するパーフェクトオーダーの割合を計算することで、企業の信頼性を図る指標として用いられています。
「納期遵守率」という指標の呼び名は日本でも一般的ですが、前述①~④の要素に照らすと、①全数を②納期通りに、という点にフォーカスされることが多く、③納品書や請求書に不備は無かったか、④納品後に不良品のクレームを受けていないか、という観点までカバーできていないケースも多いのではないでしょうか。欧米で広く浸透している「OTIF (On Time In Full)」という指標も①と②に絞った指標と言えるでしょう。
例え発注したものが全数納期通りに届いたとしても、納品書の不備や一部商品の不良は企業の信頼低下に繋がりますので、信頼性を測る物差しとしてパーフェクトオーダーはより網羅的な指標と言えます。
また、②納期通りの「納期」とは具体的に何を指すのか、という点もしばしば議論を呼ぶポイントです。パーフェクトオーダーにおいては、「顧客に対してコミットした納期(一次回答納期)」を満たせているかどうかを測ります**。これは信頼性の指標として、「約束した納期は守る」という考えが根底にあるためです。
当然、「顧客が希望した納期(希望納期)を満たせなければ意味が無い」という考えもあるでしょう。これはどちらが正しいという話ではなく、事業の特性や目標に応じて、より適切な指標を選択すれば良いのです。ただし、指標というのは他社との比較・ベンチマーキングをするためのものでもあり、「パーフェクトオーダー率」として開示されている情報が、いかなる要素・計算に基づく値なのかを正しく理解しておくことは重要です。
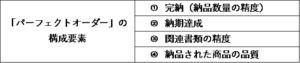
* ASCM “Supply Chain Dictionary 17th edition”
** ASCM “SCOR-DS” https://www.ascm.org
SCM用語#10:「CCC」
Cash Conversion Cycle(キャッシュコンバージョンサイクル、CCC)は、小売業や製造業などの企業が原材料や商品の仕入れ・生産などに現金を支払ってから、顧客から売掛金を回収し現金を入手するまでの日数を指す、経営指標の一つです。CCCの定義式は次のように表されます*。
CCC = 売掛債権回転日数 + 棚卸資産回転日数 ― 買入債務回転日数
CCCが小さいほど資金に余裕がある、メーカーの資金繰りが良好であるということになります。資金に余裕があるということは、積極的に投資を行えるということにつながり、企業の競争力を生み出します。CCCを改善するには、①売掛金の回収期間を短くする、②棚卸資産回転率を改善する、③買掛金の支払までの期間を長くする、といった方法が考えられます。
例えば、米アップル社のCCCは―70.9日、米テスラは4.8日(モーニングスター社調べ)と、同業他社と比較しても低い数値であり、度々ニュースでとりあげられています。 また、CCCはその大小だけでなく、同業他社との比較や過去からの推移と比較することでも活用されます。年によってその数値は変化しますが、業界平均値として、半導体などのテクノロジー業界:133.1日、消費財・小売業界:89.6日、ヘルスケア業界:122.5日、エネルギー業界:31.7日と報告されているとともに、年次でのトレンドの変化が分析されています**。資金を金額だけでなく、日数としての指標としてみることで、キャッシュフロー改善への活用が期待されます。
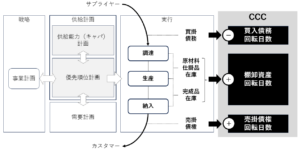
* 山口雄大・行本顕・泉啓介・小橋重信「全図解 メーカーの仕事」(ダイヤモンド社)
** J.P. Morgan 2023 August https://www.jpmorgan.com/content/dam/jpm/treasury-services/documents/strategies-for-resiliency-working-capital-index-report-2023-ada.pdf
代表筆者プロフィール
行本 顕 氏
- 1974年生まれ。APICS認定インストラクター(CPIM-F・CLTD-F・CSCP-F)、法学修士。銀行員を経て2003年より国内消費財メーカーに勤務。生産管理・海外調達他を担当。2010年~2012年にかけて米国の大手消費財ディストリビューターに常駐、S&OPを担当。
- 日本初のAPICS三科目認定インストラクターとして日本ロジスティクスシステム協会、日本生産性本部他での講演を中心にSCM普及活動を行っている。ストラテジックSCMコース第12期修了生。JILS調査研究委員会委員。JILSサプライチェーンマネジメント推進会議座長。
- 著書に「基礎から学べる! 世界標準のSCM教本」(日刊工業新聞社)「全図解メーカーの仕事」(ダイヤモンド社)他。日刊工業新聞にて「ビジネスパーソンのためのSCM講座」連載中。
さらに世界標準のSCMについて学ばれたい方へ
- 『超』入門!SCMセミナーシリーズ
『超』入門!SCMシリーズは4つのモジュールで構成されたサプライチェーンマネジメント(SCM)の入門セミナー群です。SCMの「設計・計画・実行」それぞれの業務領域に求められる「観点」と「基礎知識」の習得を目指しつつ、相互の関連性を同時に学びます。これらのモジュールはいずれも世界標準のSCMにおける世界観に準拠していますので、はじめてSCMの世界に足を踏み入れた方も、すでに実務経験を積まれた方も、受講後は本セミナーの内容を「共通言語」としてご活用いただける点にも特徴があります。
開催予定のセミナーについてはホームページをご参照ください。